Thread Rolling
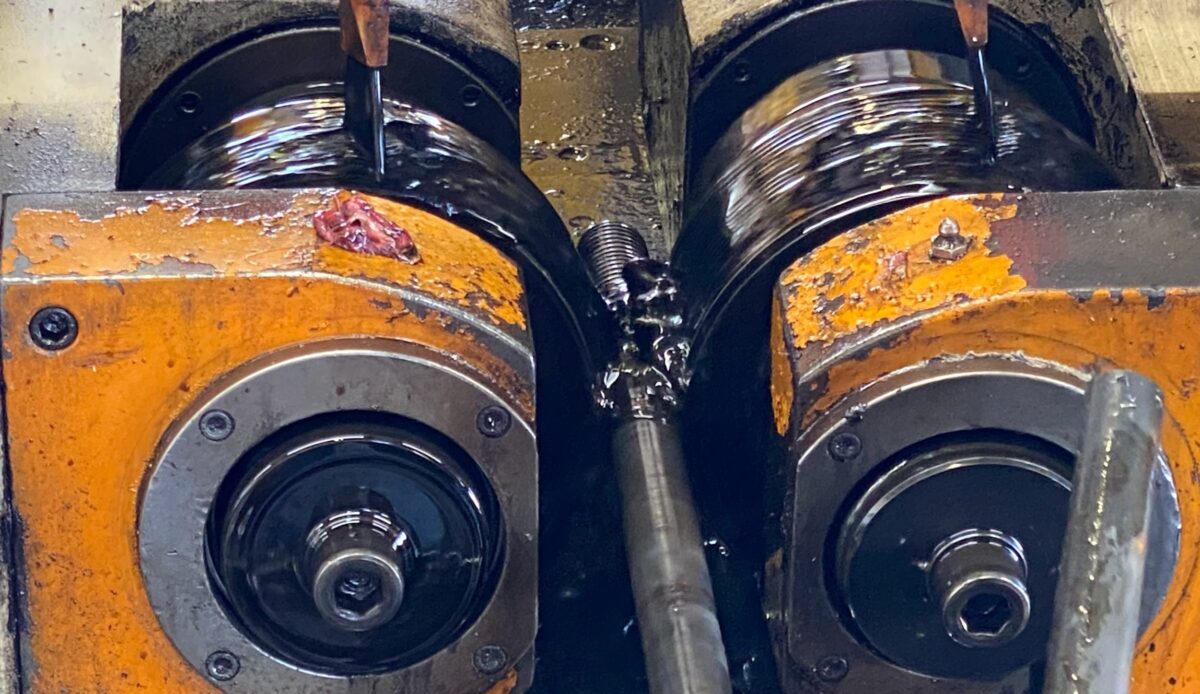
Experience The Advantages Of Thread Rolling
Thread rolling is a metalworking process that involves deforming the surface of a fastener by applying pressure and rolling it between two dies. The dies have a pattern that is imprinted onto the surface of the fastener, creating threads.
Thread rolling offers several advantages compared to other methods of thread production, such as thread cutting. Here are some of the key advantages of thread rolling:
1.
Increased resistance to loosening: The thread rolling process can produce a thread with greater contact area and a more uniform shape, which can increase the resistance of the fastener to loosening and vibration. This can make the fastener more reliable in applications where vibration or other dynamic forces are present.
2.
Increased Strength: Thread rolling creates threads by compressing the material rather than removing it, resulting in a stronger thread. The cold-forming process of thread rolling improves the metal’s grain structure, increasing its tensile strength and fatigue resistance. Rolled threads have higher load-carrying capacity and are less prone to stripping or galling under heavy loads.
3.
Improved Thread Accuracy: Thread rolling produces highly accurate threads with precise dimensions and pitch. The rolling process applies uniform pressure to the material, ensuring consistent thread geometry and pitch diameter control. This leads to better fit and interchangeability of threaded parts.
4.
Enhanced Surface Finish: Rolled threads have a smoother and more precise surface finish compared to cut threads. The rolling process eliminates the microscopic imperfections and burrs that may be present in cut threads, resulting in improved sealing, reduced friction, and easier assembly.
5.
Faster Production: Thread rolling is a high-speed manufacturing process that can rapidly produce threads. It typically requires fewer machine operations and can achieve higher production rates compared to thread cutting. This efficiency makes thread rolling a cost-effective option for large-scale production runs.
6.
Material Savings: Thread rolling utilizes the material more efficiently than thread cutting. The process displaces metal rather than removing it, resulting in less waste. As a result, thread rolling can provide material savings, especially when working with expensive or hard-to-machine materials.
7.
Extended Tool Life: Thread rolling tools, such as dies, are designed to withstand high forces and pressures. They generally have longer tool life compared to cutting tools used for thread production. This reduces tooling costs and minimizes downtime associated with tool changes and maintenance.
8.
Increased Resistance to Corrosion: Rolled threads have a denser surface structure, which enhances their resistance to corrosion and environmental factors. This makes them particularly useful in applications where protection against rust or chemical exposure is important.
Overall, thread rolling offers superior thread quality, increased strength, cost efficiency, and versatility, making it a preferred choice in many industries, including construction and manufacturing.